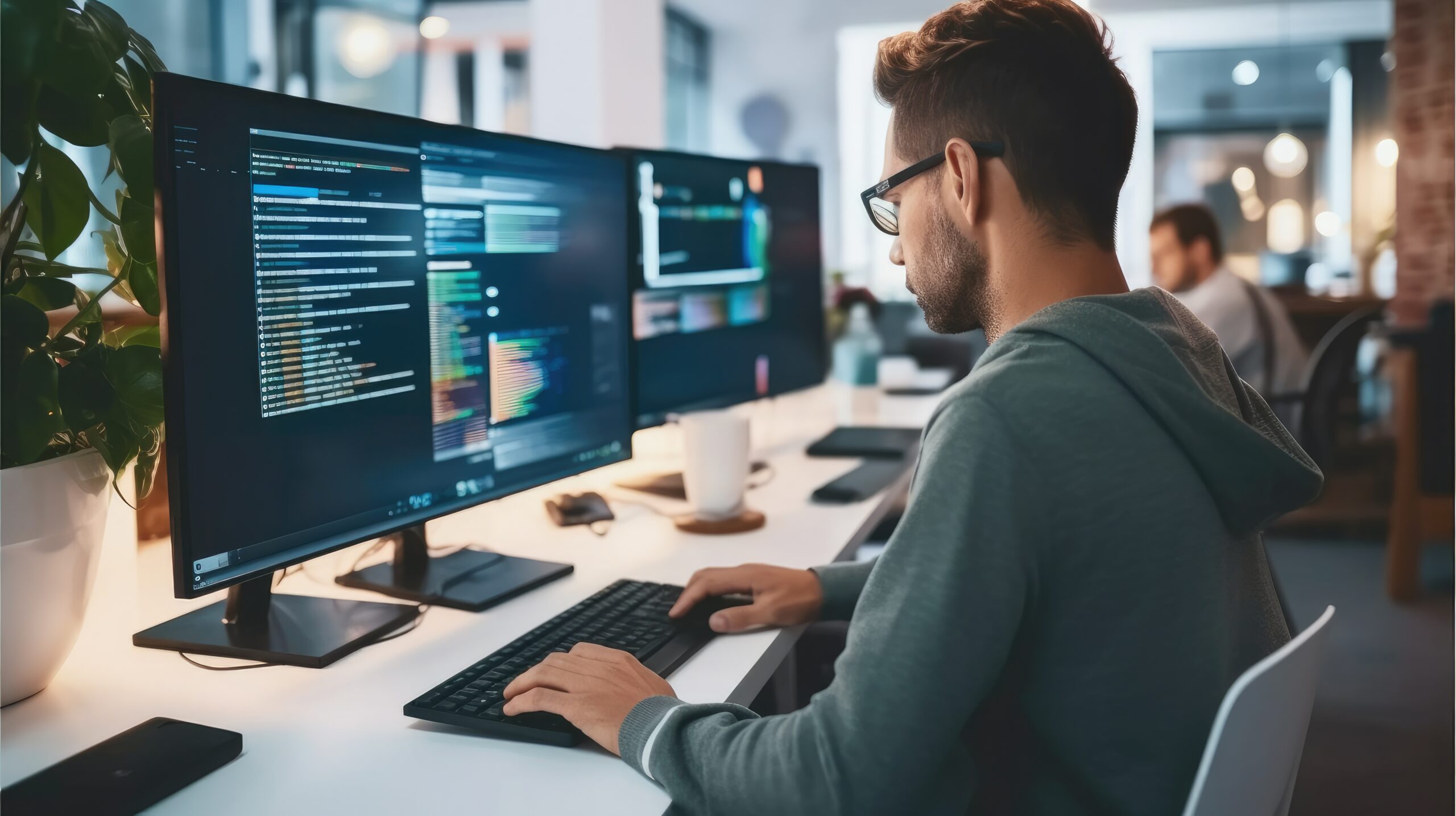
Share article:
From client to Chasm consultant Mantas describes his manufacturing career to date.
10 years ago I started my manufacturing career with one of the largest manufacturers in the world. It was there that I met Martyn King.
I had very little knowledge about manufacturing, but I was keen to develop and learn. Upon meeting Martyn, I knew I had met the ideal mentor and I will always be grateful for the opportunity I had to work with him all those years ago. Within days of watching Martyn at work I came home, took out my vision board, updated it and started manifesting being a consultant one day. At the time, I hardly knew what consulting was, but I did know the admiration I had for the work Martyn was doing and how his approach changed people’s working lives, including mine.
I became part of the Chasm team in 2021. I wake up every morning knowing that today is the day to make a difference – whether we are working in a large multinational, stand alone manufacturing enterprise or just the guidance I give to that individual whose mindset will be changed because of myself or the influence of Chasm within the client team.
In my work with Chasm across different sites, clients and challenges I am asked question repeatedly ‘Mantas, how do you lot manage to do this type of work? You are going to different manufacturers with different processes and people and need to make a big impact, how do you do it?’. Don’t get me wrong, it’s not all pretty, or easy as some may think, often it is more challenging than you can imagine to get the outcomes we pursue for our clients.
At Chasm we are all experts within our field, we have the skill set, complimentary knowledge and expertise and the unique leadership of Martyn King. My 2 key learnings from him are:
- there is nothing that cannot be fixed within manufacturing.
- the most important aspect is to concentrate on the workforce and ensure that they are all included at every step of the process so we get the sustainable change in behaviour we are known for.
Identifying broken processes, fixing operations, embedding new systems. All of this comes with a huge amount of knowledge and experience across the team. The key to the sustainability of our projects is that we ensure that communications reach everybody and that all personnel are fully involved in fixing a factory.
With opportunities to learn new skills and a different way of behaving our engagement within the client team exposes employees to engage at a different level. Chasm guide the inhouse team to take ownership of their work, line and section which delivers the change in behaviour the organisation needs.
Working with Chasm is amazing because, in everything we do, we bring passion and pride in what we do, whether it is a large deliverable or a small influence on someone’s mindset – we know every little counts.
I am often asked, what is it like working for such a reputable consulting firm? Without exaggeration I can answer – ‘It is like seeing magic happen and the best part is I am part of the magic!’