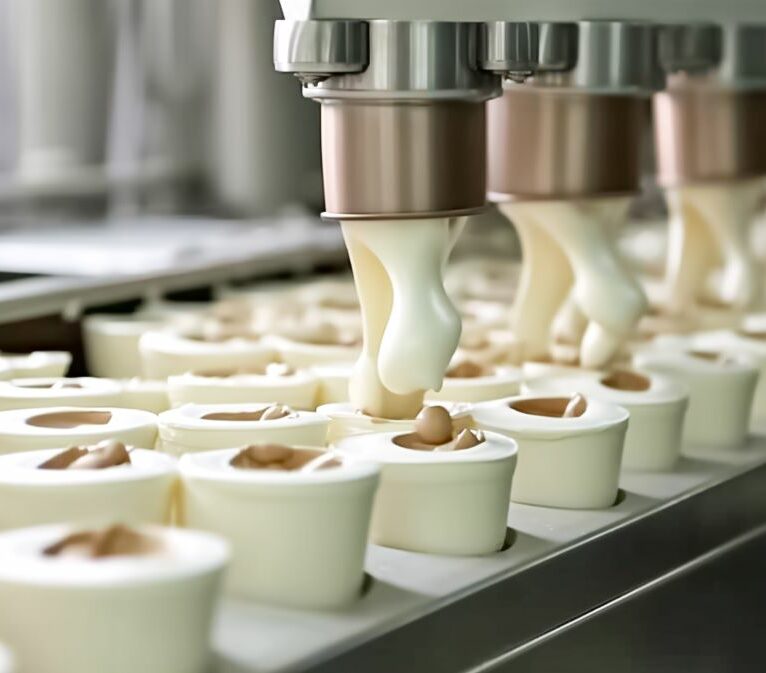
Share article:
“Cash is King” they always said, but in a world where cash doesn’t really exist anymore and big tech companies have no cash but are worth billions, I would argue that right now “Data is King”.
Technology has moved on dramatically over the last 5-10 years but there has been limited uptake on what that technology can do for the standard manufacturers and in particular food manufacturers, particularly in the area of data capture, storage, extraction & presentation.
A recent MIT insight review stated just 13% of organisations excel at delivering their data strategy, and that was from 351 data ‘experts’ in $1bn plus turnover businesses.
If they are struggling, what chance has the casual stand alone £20-100m t/o manufacturing business?
Let’s take simple Shop Floor Data Capture (SFDC) as a prime example.
In the olden days data would be collected manually on pre-printed sheets across the manufacturing facility. There would be 10s if not 100s of sheets for capturing a multitude of things;
- line performance data,
- start up machine checks,
- product traceability,
- metal & weight check sheets,
- quality documentation,
- downtime logs,
- cleaning logs…
- … the list is endless.
If you were lucky some of this data was uploaded to an Excel spreadsheet;
- 1 tab per day,
- 1 workbook per week,
- start again in week 2.
If you were even luckier somebody may have produced some reports or graphs from the Excel sheets, but as data was only stored in daily sheets any kind of trend analysis required more cut & paste to collate data.
So now you had masses of paperwork on the floor meaning operatives were doing more admin than operating. Supervisors & shift managers were spending hours analysing Excel spreadsheets trying to understand the cause of the data and doing less managing. Hands up if you had 7 years of archive records taking up valuable pallet space in your warehouse.
We have the world of data seemingly at our feet, infinite possibilities of high performance data & AI, smart factories ready for infinite analytics.
With such opportunity why are so many organisations taking the lazy route and just automating the data capture they had before. I see you, replacing the A4 paper with a few iPad’s, some TV displays in the factory, a few colourful charts and hey presto all is resolved, right?
No and reason is The data is no better than it was before, its just collected faster. Because the data is still ‘manually’ collected onto said iPad there is limited collection points (running / not running). The data analytics is no better, just the charts are prettier than before. The culture of the organisation and the ‘management control system’ is no better. The competencies of the people are no better than before. So even if you opt for one the many Connected Workforce solutions out there, installing it without building the skills & competencies, without understanding structure, roles & responsibilities, without building robust data analytics and reporting, you are just polishing the turd,
In the same MIT review, organisations stated their top priorities over the next 2 years fell into 3 areas: Improving data management, enhancing data analytics and Machine learning, and expanding the types of enterprise data.
So, given we have technology to link virtually every machine in your factory to a data collection solution, that will give granular data on machine performance, downtime causation, energy usage, weights, product integrity and allow paperless audits. That can link to your ERP system, T&A, CMMS and every other system to share information and create a lake of data for analytics, validation, BI, machine learning and the pretty graphs, why would we not do it?
The simple reason is one of 2 things. Laziness and understanding. People are inherently lazy and just looking to solve the immediate problem in front of them, and for many it ticks a box to put a basic electronic SFDC in place. The factory won’t get any better long term. There will be a short-term improvement from the hawthorn effect, no different to any other new installation. I have seen countless sites install such solutions and see 15%+ improvements in efficiency only for it all to drop off (and sometimes worse) in 9 months.
Understanding is a whole different ball game. The rate of change in technology and what it can do is scary to say the least and not for the faint hearted. That’s why people choose to get outside help from people who know. That’s why people call Chasm.