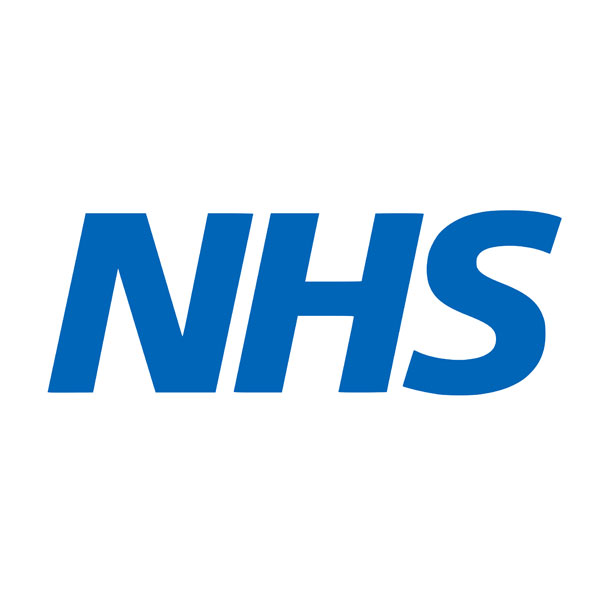
Share article:
Following success with a similar project previously Chasm were engaged to support business wide improvements in efficiency of Customer service, depot staff, vehicle routing, driver efficiency and system integration.
At the core of the project was value stream mapping the core service delivery routes and understanding the base efficiency of all the personnel in process.
Customer service – taking calls, processing orders, manifesting driver routes and planning loads covering delivery, collection, service & adaptation
Warehouse – load picking, vehicle loading, unloading, put away
Hygiene – cleaning used equipment and put away
Drivers – routing & efficiency.
The core project aim to increase the efficiency of the support processes such that drivers and vehicles maximised loads and delivery times, that’s where the money was.
Working closely with the group IT team to build integrated solutions and developing a standard model to roll out across multiple depots across the UK.
Overall 25% efficiency improvement of technicians responsible for delivery, service and adaptations at end user properties.
- 13 UK depots covering 130+ vans and technicians
- Redesigned the customer services processes to reduce lead times, improve call handling and increase customer satisfaction
- Improvement in stock, warehousing and purchasing processes to support the flow of materials from supply to end user
- Installed robust KPI suite to monitor and measure performance both at depot and centrally
- Additional 5 UK contracts won after the success of the initial projects
This project showcased the depth of the Chasm team, it wasn’t a normal factory efficiency project, it required adaptation of core tools for a whole new environment.
At the core was an ESLH (Earned Standard Labour Hours) model, if you would like to see more have a look at the downloads section.