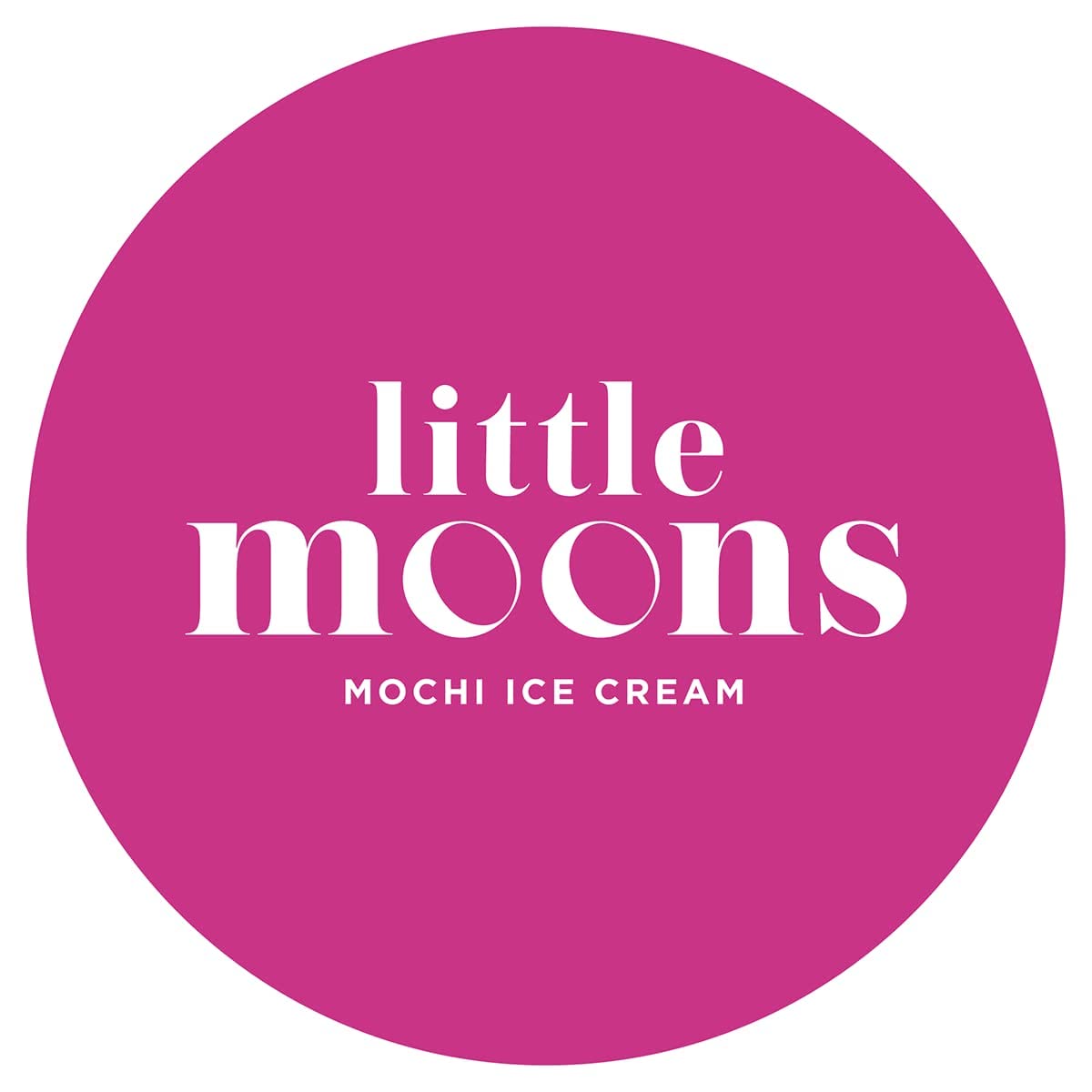
Share article:
Supply Chain Management at Little Moons
Supply Chain Management is a key area for start-ups to get right.
Here is a fairly detailed summary of how Chasm tackled supply chain management with the team with start up sensation Little Moons. Chasm worked with Little Moons, the food manufacturer at a time when they were experiencing growth of 500%, after going viral on TikTok, which makes this a very exaggerated story. However, I hope it serves to give a way to compare your own factory structure and manufacturing approach and proves that you can implement change whatever the weather!
The start up initially requested help to scope out a Warehouse Management System (WMS) as they had major issues with
- stock accuracy
- stock usage
- swings in variances
It was agreed Chasm would process map (Brown Paper) the supply chain site processes from Sales Orders to Despatch so we could pick up all the material and stock transactions within the food manufacturing business.
Along with the major problem of them having no ERP system on which to integrate the WMS, we also found out they lacked basic processes for:
- demand planning
- factory scheduling
- material requirements (MRP)
- factory performance
- supply chain processes
- continuous improvement
- finally, there was a fundamental lack of competencies with which to operate
Just for a bit of context at this time with the increased in demand (500%) there was an urgent need to add extra food manufacturing capacity through shifts, new machinery and efficiencies.
The project continued and expanded with several workstream specifically:
- Upgrade ERP system from Sage 50 to Sage 200
- Scope out and install a WMS integrated with the ERP
- Build a demand & planning tool to convert sales forecast into manufacturing plans
- Build capacity modelling tool aligned to and S&OP process
- Build a scheduling system for the production lines
- Build and install an MRP (material requirements planning) system for material demand to site
- Build a process for Work Orders to control material issues to the factory floor
- Build a labour planning tool aligned to the schedules to support labour productivity
- Install a Management Control System (MCS) in the factory – how the execute the plan and talk about daily & weekly performance
- Build a SFDC (shop floor data capture) system to monitor and control production data
- Install a Stock cycle counting process with KPIs to drive stock accuracy and transactional disciplines
- Install a continuous improvement process for £ savings
- Build a full competency framework with training & development of key operational employees
- Support a shift change to 7 day working
- Set up EDI for order processing with 20 UK / EU retailers
- Set up EDI with 3PL for data transfer
In addition, when building the ERP system Chasm had to undertake a significant amount of work on ‘Master Data’ including:
- Building Bill Of Material (BOMs) for upload into Sage
SKU rationalisation process to remove offline tracking of Finished Goods - Build robust Unit of Measure (UOM) into data so that purchases quantities match stocking quantities
- Introduce stock traceability through ERP
- Implement data attributes to stock movements to remove 100s of hours of offline admin
In summary it was like performing open heart surgery on a patient whilst they were running the London Marathon. At the time of writing we are moving onto phase 3 which is transferring all we have built and installed into a new facility.
“…without Chasm we would never have coped with the uplift in volume, our factory and systems were not good enough.”